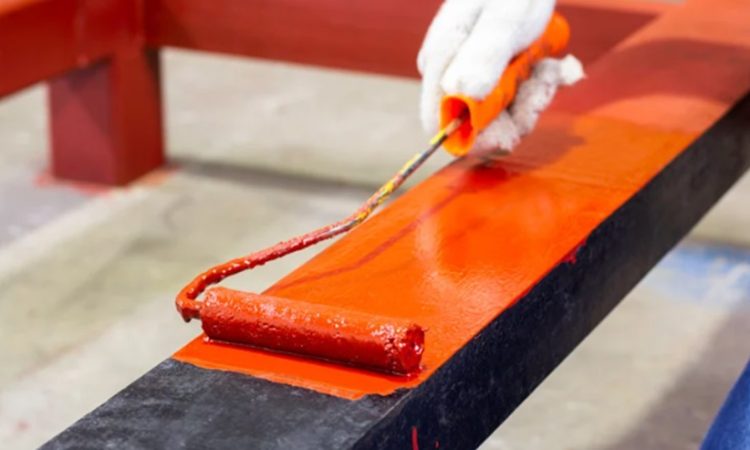
Metal surfaces are widely used in commercial and industrial environments due to their strength and durability. However, one of the biggest threats to metal is corrosion, which can compromise structural integrity and lead to costly damage. To extend the lifespan of metal, it’s essential to use protective coatings. Among the most effective options is direct-to-metal paint, which provides a reliable barrier against moisture and environmental elements.
The Science Behind Metal Corrosion
Corrosion typically occurs when metal is exposed to oxygen, moisture, or chemicals for extended periods. The reaction causes rust and surface degradation, especially in outdoor or humid environments. Once corrosion begins, it can spread quickly and lead to premature failure of metal structures or equipment.
Advantages of Direct-to-Metal Paint
One of the major advantages of using direct-to-metal paint is that it eliminates the need for a separate primer. This type of paint is specially formulated to adhere directly to metal, creating a strong protective seal. The paint forms a barrier that prevents moisture and oxygen from coming into contact with the metal surface, which is critical for stopping rust before it starts.
This not only saves time but also increases application efficiency in commercial settings. Additionally, it adheres well to both ferrous and non-ferrous metals, making it versatile for a wide range of industrial applications.
Added Durability for Industrial Surfaces
Direct-to-metal paint is designed to withstand tough environments. It resists UV rays, chemicals, and abrasion, making it ideal for warehouses, outdoor structures, machinery, and other metal assets exposed to extreme conditions. In fact, coatings like these are essential in protecting industrial metal surfaces, especially those in high-traffic or weather-prone areas.
When planning maintenance or construction projects, factoring in long-term protection is vital. That’s why investing in premium coatings tailored for metal ensures greater value and lower maintenance costs over time.
Surface Preparation and Application Considerations
Although direct-to-metal paint simplifies the coating process, surface preparation is still important. Metal should be cleaned of dust, oil, and loose rust to ensure optimal adhesion. A smooth, clean surface enables the paint to bond effectively and form a uniform coating. This enhances both the appearance and functionality of the paint layer.
While this type of paint is a professional-grade solution, it’s important to ensure proper application techniques and equipment are used. Employing skilled professionals guarantees that the finish is even, durable, and long-lasting—maximizing the product’s performance benefits.
Long-Term Benefits of Direct Metal Coating
Beyond just corrosion resistance, direct-to-metal paint enhances the aesthetic value of metal structures. It provides a smooth, glossy, or matte finish that improves the overall look of equipment and buildings. Over time, this paint helps reduce maintenance needs, prevents structural failure, and preserves the investment in your metal assets.
For industries where asset reliability is key, coatings that ensure long-term durability are indispensable. They protect from the inside out, serving as both a shield and an enhancer for metal components.
Conclusion
Choosing the right protective coating is critical when it comes to preserving the integrity of metal surfaces. With its superior bonding ability and corrosion resistance, direct-to-metal paint delivers professional-grade results that last. Whether you’re protecting a metal warehouse frame or industrial machinery, prioritizing coatings that support protecting industrial metal surfaces helps maintain performance and extend service life. To better understand its significance for harsh environments, explore why direct-to-metal paint is essential for outdoor metal surfaces and how it supports long-term infrastructure goals.